Electro Permanent Magnetic Quick Change System
Revolutionize Your Moulding Process with Our Electro Permanent Magnetic Quick Change System – Faster, Stronger, and More Efficient
Quick change system
The HQMC Magnetic Clamping System (Quick Mold/Die Change System), uses optimised unique electro permanent magnetic clamping technology, for the clamping of moulds and dies for plastic injection moulding machines and metal stamping presses. Change of mould, 3 minutes ready.
In this way the change time of moulds and tools is drastically reduced up to 95%. This system consists of 2 magnetic plates, fixed and stationary, man-machine interface, electrical control box. Size and geometric shape of the magnetic plates can be freely designed as requested by the customer.
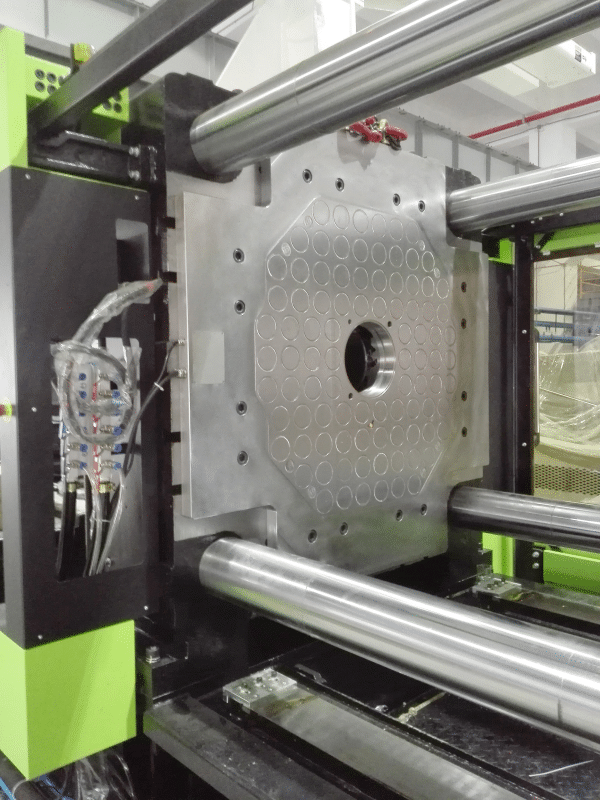
Advantages of Magnetic Quick Change Systems (HQMC)
1. Provides 20% more magnetic force than conventional magnet systems
2. Full metal surface is oil and waterproof, ensuring maximum durability and longevity
3. Super thin and solid construction is perfect for use with injection moulding machines ranging from 50-4000 tons
4. Higher efficiency in mould changes – All moulds can be changed in less than 3 minutes
5. The uniform clamping force ensures that there is no deformation of the mould during the production process.
6. Flexibility allows for all moulds, regardless of shape and size of the mould base plate, to be clamped without adjustment
7. Eliminates the need for many clamping tools and allows for the complete area of the machine plate to be used by eliminating clamps
Download our brochure
Products
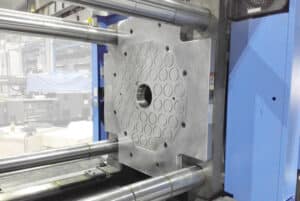
Magnetic Quick Change Systems for Injection Moulds
Magnetic clamping plates reduce mold changeover time by 90%, enabling safe and ergonomic mold changes by a single operator. No mold modifications are needed, as any shape or size can be safely clamped.
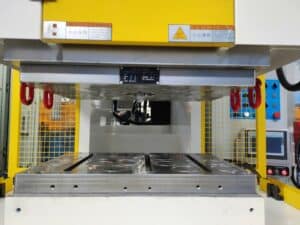
Magnetic Quick Change Systems for Dies
Magnetic clamping plates can decrease die changeover time by 90%, allowing one operator to safely and ergonomically perform the task.
The highest safety standard
1. CLOSED MOULD DETECTION
The MAG cycle can only be performed
when a build-up of pressure is detected.
This ensures that both mould halves fit
100% against the respective magnet plates
when the MAG cycle is performed.
2. MAGNETIC FLUX DETECTION
Release for production is only obtained if the measured magnetic flux, after magnetization, reaches the standard minimum safety value. If this is not the case, an error is indicated. If during the injection process the magnetic flux value decreases minimally, the machine stops immediately
3. TEMPERATURE DETECTION
To prevent the magnetic plates becoming too hot, which reduces the total magnetic force, the magnetic plates are equipped with a temperature sensor. When the temperature gets higher than the pre-set value, the automatic
4. MAGNETIC FLUX DETECTION
During the MAG and DEMAG cycle, the current pulse is monitored by the current detection sensor. Only when the set value is reached, a successful release is allowed.
5. MOULD DISLOCATION DETECTION
The position of the mould is monitored during production. If due to circumstances a small shift of the mould occurs, the machine stops immediately.
6. DISTANCE DETECTION
The proximity switch ensures that the DEMAG cycle can only be performed if the distance between the die and the magnetic plate is less than 0.2 mm. In addition, the automatic production process stops immediately when a distance 0.2 mm is detected between mould and
magnetic plate.
7. INTERFACE CONTROL SYSTEM
Only when all detection sensors are in normal operation, the fixed and movable side have been successfully magnetized, and the safety key has been placed in the injection position, the automatic production process can be started. Any other condition will result in ALARM, stopping automatic operation of the machine
8. SAFETY KEY SWITCH
The safety key is used to select setupor production mode. To demagnetise, the LOCK and DEMAG button must be pressed simultaneously. Demagnetising is not possible during the automatic production process.
Download our brochure
Gain valuable insights into the benefits, applications, and technical specifications about Electro Permanent Magnet Quick Change Systems. Fill in the form below to receive the brochure directly to your email.
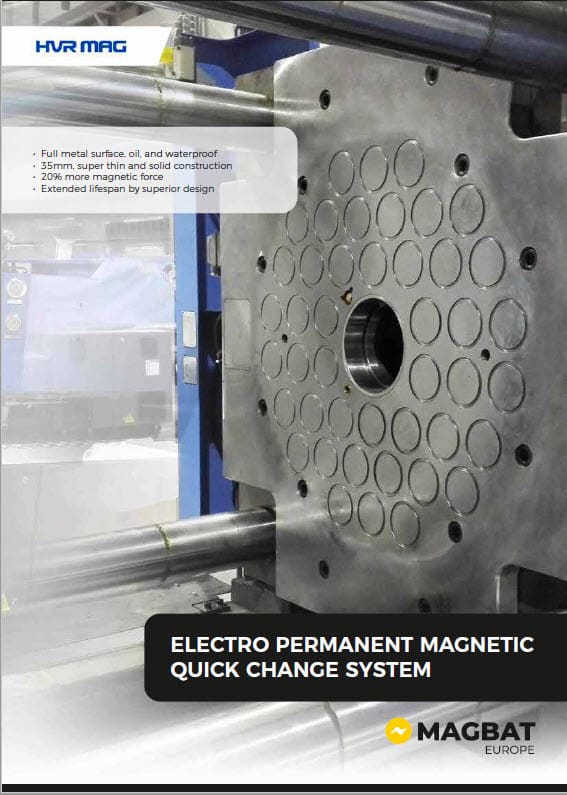
Gain valuable insights into the benefits, applications, and technical specifications about electro permanent lifting magnets.
FAQ about magnetic quick change system
What is the electro permanent magnetic quick change system?
The electro-permanent magnetic quick change system for moulds and dies is an advanced technology that allows for swift and efficient changing of moulds and dies in manufacturing processes. It utilizes a combination of electromagnets and permanent magnets to secure and release the tooling, reducing downtime and improving productivity.
How does the electro permanent magnetic quick change system differ from traditional clamping systems?
The electro permanent magnetic quick change system provides several advantages over traditional clamping systems. It provides an uniform clamping force, avoiding mould deformation during the production process. Additionally, the flexibility of the electro permanent magnetic quick change system allows for all moulds, regardless of shape and size of the mould base plate, to be clamped without adjustment. This eliminates the need for many clamping tools and allows for the complete area of the machine plate to be used by eliminating clamps.
Can the HQMC electro permanent magnetic clamping system be used with all types of injection moulding machines?
The HQMC electro permanent magnetic clamping system is specially designed for injection moulding machines ranging from 50-4000 tons.
How does the HQMC electro permanent magnetic clamping system compare to traditional clamping systems in terms of efficiency?
The HQMC electro permanent magnetic clamping system provides higher efficiency in mould changes compared to traditional clamping systems. Smaller moulds can be changed in less than 3 minutes, while larger moulds can be changed in just 20 minutes or less – a significant reduction from the traditional 2-hour or more process.
Can the HQMC electro permanent magnetic clamping system be used with all types of moulds?
The flexibility of the HQMC electro permanent magnetic clamping system allows for all moulds, regardless of shape and size of the mould base plate, to be clamped without adjustment. This eliminates the need for many clamping tools and allows for the complete area of the machine plate to be used by eliminating clamps.
Achievements
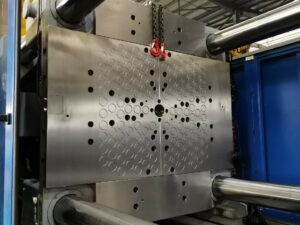
QUICK CHANGE SYSTEM FOR A 600 TON INJECTION MOLDING MACHINE
The installation of an electro permanent magnetic (EPM) quick-change system on its 600-ton injection moulding machine provided our customer with immediate and significant benefits.